Product Testing: 5 key differences between lab tests and on-site tests during inspection
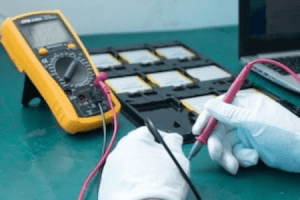
There is often confusion between Product Testing in a laboratory compared with testing carried out during an inspection. While both have a common objective to ensure the conformity of goods, they approach that task from different perspectives and require particular expertise.
General definition
• Laboratory (lab) testing ensures that goods conform to the national regulations of the country of importation. • A product inspection ensures that goods conform to the client’s requirements, product specification, and the requested quality level. The process consists of visual checks in addition to basic product testing, also called on-site testing.
Product testing during an inspection vs. lab testing: 5 differences
1- Product Testing Environment
Controlled environnement
Laboratories perform tests in a controlled environment under conditions defined by the applicable standard. Testing equipment is regularly calibrated to ensure the most precise and reliable result. The testing laboratory will ensure they perform the analysis under the required conditions and can then certify the compliance of the product with the standards.
Basic conditions
As most of the testing equipment is large and heavy, quality inspectors will only perform some of the tests if the necessary equipment is available at the factory. They will verify the latest calibration date to evaluate the reliability of the result. Nevertheless, the test is usually performed under basic conditions which may not meet all those required by the standards. For example, when the humidity or temperature is high in the testing room, the result of a moisture test varies. Therefore, the result of this test during a product inspection can only be used as a reference. It cannot be used to certify conformity to standards because of the uncontrolled environment.
2- Product Testing Purpose: Legal Compliance vs. Customer Quality
Standards and regulatory requirements
Lab testing verifies the safety of a product or compliance with applicable standards and regulatory requirements in the country of destination of the goods. However, just because the goods meet the requirements of mandated tests, it doesn’t mean they are suitable for end consumers. Compliance is but one part of Quality when it comes to what consumers expect.
Your requirements
Product inspection assesses the quality of the manufactured goods based on the client’s requirements which reflect the end user’s expectations of the product. The process can’t necessarily ensure compliance with standards, but it does guarantee that products meet specifications deemed important to the end consumer.
3- Product Sampling
Few pieces
Due to the expense and often destructive nature of the tests, far fewer samples undergo laboratory testing compared with the number examined during an inspection.
Tens or hundreds
For product inspection, quality inspectors use International standard ISO 2859-1 standard (commonly called AQL tables) to determine the number of samples for examination. For large lots, they may need to test hundreds of samples. For example, for an order of 10,000 soft balls for babies to be exported to Europe, a laboratory needs 6 samples to verify compliance with EN 71 and ISO 8124 standards. When a quality inspector performs a pre-shipment inspection for the same order, he checks 200 pieces (based on the General Inspection level II) and tests between 5 to 200 products depending on the complexity of the tests.
4 – Product Testing Frequency
Once or twice during the product life cycle
Lab testing is usually only done once, at the beginning of a new project, and then maybe once during production. The initial tests ensure the supplier has the capability to comply with the standards. The second test verifies the materials, product design, and final product comply with relevant standards when they are manufactured on a larger scale. Most companies don’t usually order lab tests for repeat orders as they assume the supplier will use the same material and repeat the design as per the first lot.
Every time a new batch is manufactured
Product inspections should be performed every time a new batch is manufactured, and preferably at different stages of the production process. Even if the design and the materials used for the manufacturing of the goods remain the same, and the product is initially compliant with specific standards, it does not mean the quality will continue to be consistent over time or that you won’t suffer any production delay. Regular inspections are necessary to ensure the product quality continues to meet consumer expectations, and to avoid supply chain disruption.
5. Time Required for Product Testing
Lab testing always takes longer than a product inspection.
Results aren’t available as soon as those from the product inspection for the following reasons: • Tests are usually more detailed and analyze every component and material used to manufacture the product, including paint. • The tests are more complicated and take longer (it may involve some chemical manipulations, or require a test to be repeated over several hours or days) • Independent third parties in charge of the product testing are usually off site. The quality inspector is responsible for sending randomly selected production samples to them.
Remark: Laboratory testing can contribute to longer lead times. When delivery deadlines are tight, you should plan for laboratory tests as far ahead as possible, or results might not be available before the product is shipped. For example, when requesting lab testing to verify toy compliance with EN 71 part 1, 2, 3, the laboratory needs 5-7 days to test and deliver the final result. To obtain a CE certificate, required by the European Union takes 2-3 weeks. In comparison, a toy product inspection is performed within one to two days after placing your order. Your products are quality controlled, tested, and a detailed report is sent to you within 24-48 hours.