What to do after a failed inspection
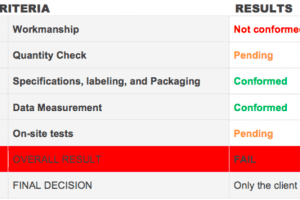
The pre-shipment inspection is the last chance for the buyer to detect defects and identify unacceptable quality before the shipping of the goods. What to do after a failed inspection? Buyers can reject lots before they are shipped but there are other alternatives to take into consideration.
Buyer’s options after a failed inspection – what to do with the goods?
5 most common options
There are various answers to the question, what to do after a failed inspection. Essentially there are five options to choose from:
- Refuse the goods (seldom a choice)
- Ask the vendor for a discount and ship the goods
- Ship the goods anyway
- Ask the vendor to rework products
- Ask the vendor to sort out defects
Option of replacing / reworking goods
Most buyers ask their vendor to rework or replace faulty goods even though it delays the shipment. The vendor usually agrees on it. Afterwards the buyer has two choices:
- Believe the vendor did improve things, pay and ship the goods (risky)
- Re-inspect the goods to verify whether or not they have been reworked properly, and no new defects appear during the reworking process (most reliable)
For the re-inspection (usually paid by the supplier), the standard pre-shipment inspection protocol is used to give another general overview of the quality of the goods. Most third party inspection companies send another inspector, different from the previous inspection. This method identifies all kinds of defects and confirms whether or not the rejected defect(s) have disappeared.
As a matter of fact, by reworking the goods, there is always the risk that new defects appear, only the pre-shipment inspection will allow those to be identified.
Option of sorting out defects
It is possible to request a third party inspection company to sort the defects when only 1, 2 or 3 defect types caused the inspection to fail. As it focuses on few defects only, a much higher quantity of goods can be inspected within the same amount of time, ensuring a higher representativeness of the sample. It gives a better idea of the importance of those defects within the overall order. Moreover, the buyer has two choices:
- Request the rework of the sorted goods and follow the choices of replacing/reworking the goods as above
- Ship only the acceptable goods
The defect sorting is an alternative option of the reworking of the goods, however both options are complementary and can be combined.
And you: what do you do after a failed inspection?